Selecting a hot melt dispensing system
Six easy start up steps for selecting a hot melt dispensing system.
For an application questionnaire and worksheet, please email us to [email protected]. We'll email a sheet which can be faxed or emailed back. We'll then recommend a full system.
|
|
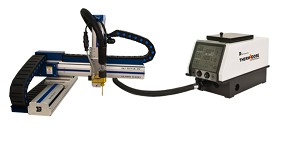
|
1 Selecting a Tank Controller for an Automated System
Tank controllers are most popular for medium-volume production. The
recommended system is the HM14 followed by the higher volume HM34. The
HM12 is not recommended for automated production due to its analog
controls.
2 Selecting a Tank Controller for a Manual System
Select the appropriate tank capacity controller. All systems (HM12,
HM14, HM34) are suitable for manual dispensing. Select a floor-stand
option if required.
3 Selecting a Heavy-Duty Braided Heated Hose
Select a hose diameter suitable for viscosity and flow rate. The
maximum hose length possible varies per system. A hose over 16ft
(4.87m) requires a 220/230V unit. Hoses are PTFE - stainless steel
braided. WARNING: Always allow extra length for corners, a minimum of 16" (406mm) dia. per bend.
4 Selecting an Applicator-Valve for a Manual System
Applicator-valves are available as all-electric and pneumatic options
for fixed mounting or as hand-guns and vertical grip applicators.
Nozzles are selected for beads, swirl and spray. Valves are operated by
trigger or foot switch.
5 Selecting an Applicator-Valve for an Automated System
The applicator-valve set for a robot is usually a single head
all-electric type and a nozzle for dispensing shots or beads. In box and
carton manufacture, a multiple-outlet applicator-valve head is used
for top and bottom sealing of folds. Swirl pattern nozzles and spray
heads are employed to cover wider areas or coat surfaces.
6 Selecting a Timer or an I/O
An I/O interface is a simple electronic handshake box that enables an
automated line or robot to communicate with a tank controller. Timers
are attached to an auxiliary connector on the tank controller and used
to control either 2-or 4-event cycles that may be required in
conveyor-fed operations, for example box and carton manufacture.
|
Air-Powered
Dispensers * Industrial Dispensing Components * Syringe Barrels *
Cartridges * Tips * Nozzles * Robots * Mixers * Hot Melt Dispensers * Adhesives
* Epoxies * Cyanoacrylates * UV Cure * Anaerobics * Epoxies * Silicones
* Packaged Components * Techkits * RatioPacks * Hingepacks * | |
|